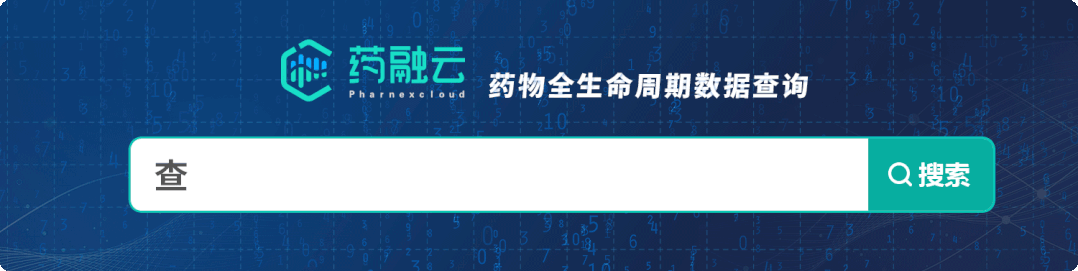
制粒是将粉状、块状、熔融液、水溶液等状态的物料经过加工,制成具有一定形状和大小的颗粒状的工序。对于粉状的物料来说,制粒的目的:①改善物料的流动性,便于进行后面的工序;②防止粉体中各混合成分的离析;③减少粉尘飞扬以及在容器器壁上的粘附;制得颗粒可以是最终产品也可以是中间体,作为最终产品,制粒还能调整堆密度,改善溶解性能;作为中间体,还能改善片剂生产中压力的匀匀传递等。制粒也分为不同形式,最主要的是湿法制粒和干法制粒,其它还有喷雾制粒等。其中湿法制粒应用最广泛,本篇主要关注湿法制粒工艺要点。
湿法制粒是在粉状物料中加入适宜液体润湿剂制备颗粒的方法。常用的润湿剂可以是水、乙醇、等其他溶剂,也可以是粘合剂以一定比例配制的溶液。粉末通过粘合剂的架桥或粘结作用聚结在一起,并在机械外力的作用下分离为具有一定大小和形状的颗粒。根据作用机械外力的方式,湿法制粒可以分为以下几类:

其中高速搅拌制粒是生产上应用最多的制粒方式,因为它在一个容器内就能实现混合、捏合、制粒的过程,与传统的挤压制粒相比,具有省工序、操作简单的特点。与流化床制粒相比,具有控制参数简便,工艺重现性高的特点。高速搅拌制粒机设备主要由容器、搅拌桨、切割刀组成,见图1。
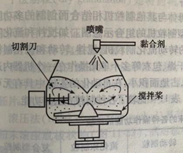
图1高速搅拌制粒原理[1]
湿法制粒的核心部件由这几个部分组成,但在实际使用中,不同品牌的的设计,仅搅拌桨的设计就千差万别。在小试到工艺放大过程中,工艺开发者就可能面临不同品牌带来的差异风险。从高速搅拌制粒原理来看,组成一套完整的湿法制粒操作的参数如下:
(1)物料性质和装量:不管是哪种设备,载料量应设计在设备能容纳的合理区间,这也能规避放大过程中由于载料量不合适导致的失败风险。例如一台设备说明的合理载料量为40-70%,条件允许的话,避免选择边界的装载量,约50-60%是比较合理的,此外,湿法制粒的装载量还要考虑浆液用量,避免浆液加入后制粒空间不足。
(2)预混阶段:预混阶段是为初步将原料或其中的关键辅料混合均匀,预混阶段通常开搅拌桨转速即可,若存在辅料流动性差、结团现象,适当开启剪切参数可尝试用于改善预混阶段混合效果。湿法制粒工艺预混阶段通常不要求作混合均匀度取样考察,按照《口服固体制剂混合均匀度和中控剂量单位均匀度研究技术指导原则》中混合均匀度要求,将在总混阶段和中控剂量单位工序重点取样考察。
(3)制粒参数:工艺放大过程除保持装载相同比例的物料降低风险外、制粒参数也常常需要考虑,制粒参数包括搅拌桨转速(rpm)和切割刀转速(rpm)。由于放大批次单独考察制粒参数物料消耗巨大。一般小试批量与放大批设备品牌若一致,供应商可以提供他们不同级别设备的放大参数调整区间,当然这里是基于他们的标准物料得到的参数。若没有供应商提供的参数支持,也可借鉴较接近工艺品种的已有参数来放大研究。若以上都没有,这里引入一个弗劳德系数(Froude数)供参考:
Fr=n2r/g,
其中,n:搅拌桨转速,r:搅拌桨半径,g:万有引力常数。Froude数和转速的平方以及搅拌桨半径的乘积成正比,在小试阶段采用低Froude数来实现制粒,因为相同转速下,搅拌桨半径越大,线速度越大,设备越大,转速越低。
(4)制粒时间:此处所说制粒时间,通常分为两个阶段,包括加液时间和制粒时间,加液时间由加液量和加液方式来决定。在小试阶段处方已考察出合适的加浆量和该品种加浆的方式,在小试批研究的基础上,若品种适合快速加浆,通常在几秒到几十秒间加液完成,则制粒时间与加液时间合并计算也未尝不可;若品种对加液速度有要求,如长至几分钟加液,则通常将加液时间和制粒时间分开计,这是两个阶段。制粒时间通常会有两种影响,第一种是制粒时间过短润湿剂未充分分散,第二种是制粒时间过长颗粒长大性质变化,制粒工艺应控制在合理的时间窗口内完成。
(5)粘合剂的用量:粘合剂有两种加入方式,干粉加入和配浆形式加入。如果以干粉形式加入,实验室阶段考察合适粘合剂的加入区间,由小试批到工艺放大批只需等比计算粘合剂的用量,干粉加入优点是粘合剂用量等比放大,方便计算;风险是由于批量、设备等变化粘合剂本身的润湿程度可能发生变化,进而影响颗粒的性质。因此首次进行工艺放大时,润湿剂的用量需要根据软材的状态作调整考察。第二种是粘合剂以溶液形式加入,优点是可以规避粘合剂没有均匀润湿的风险,另一面则需要考虑粘合剂的浓度、加入容器管道的残留、润洗等,还有工艺放大后由于润湿剂黏度等性质变化带来的设备可操作性。
结语:湿法制粒工艺虽然是作为较常规的工艺广泛应用到制剂技术中,但无论在成品还是中间体中都扮演着重要的角色,每个品种对具体工艺的要求也千差万别,面对的问题也不尽相同,但工艺开发始终遵循将风险控制在产业化阶段之前的原则。
参考文献
[1]崔福德,龙晓英.药剂学[M].北京:人民卫生出版社,2011
相关阅读:
<END>
收藏
登录后参与评论