近几年来,生物制剂发展迅速,尤以病毒、疫苗、蛋白、多肽以及核酸火热,因其对热不稳定,故制剂过程中常将其冻干后保存,使最近冻干技术备受关注。
什么是冻干呢?
冷冻干燥,全称真空冷冻干燥,简称冻干,是指把含有大量水分的物料预先进行降温,冻结成冰点以下的固体,在真空条件下使冰直接升华,从而去除水分得到干燥产品的一种技术。因为利用升华达到去除水分的目的,所以又称升华干燥。
冷冻干燥有下列优点1,2:
一.冷冻干燥在低温下进行,因此对于许多热敏性的物质特别适用。如活性蛋白、多肽和微生物制剂等。
二.在低温下干燥时,物质中的一些挥发性成分损失很小,适合一些化学产品、药品和食品干燥。
三.在冷冻干燥过程中,微生物的生长和酶的作用无法进行,因此能保持原来的性状。
四.干燥能排除95-99%以上的水份,干燥后产品能长期保存不变质。
五.由于在冻结的状态下进行干燥,体积几乎不变,保持了原来的结构,不会发生浓缩现象。
六.由于干燥在真空下进行,因此一些易氧化的物质得到了保护。
七.干燥后的物质疏松多孔,呈海绵状,加水后溶解迅速而完全,几乎立即恢复原来的性状。
因此,冷冻干燥目前在医药工业,食品工业,科研和其他部门得到广泛的应用。
冻干机介绍
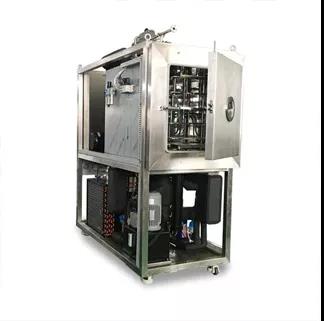
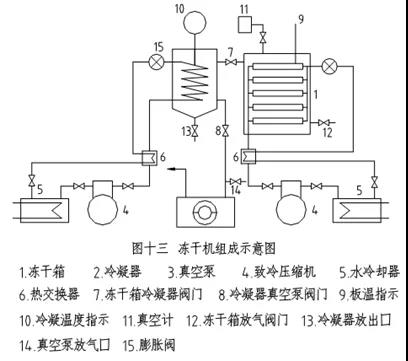
冷冻真空干燥机简称冻干机,由制冷系统、真空系统、加热系统和控制系统四个部分构成2。如上图所示:
制冷系统由冷冻机、冻干箱和冷凝器的内部管道组成;主要对冻干箱和冷凝器进行制冷,冻干箱的温度可以低至-55℃左右。
真空系统包括冻干箱、冷凝器、真空泵、真空管道和阀门等;提供对制品进行升华干燥所需要的真空。
加热系统可以分为电加热法、辐射法和循环的中间介质加热法;用于对制品加热升华其水分,冻干箱的温度可升至+80℃。
控制系统主要是各种控制开关、仪表、自动装置等,对冻干机进行自动或手动控制。
冻干的原理
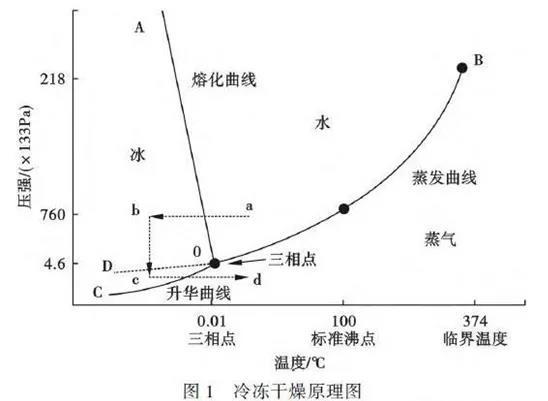
冷冻干燥的原理可以用水的三相平衡图加以说明。
众所周知,水有固态、液态、气态三种相态,如图所示,图中OA为冰-水平衡曲线,OB为水-水蒸气平衡曲线,OC为冰-水蒸气平衡曲线,O为冰、水、水蒸气的三相平衡点,温度为0.01℃,压力为4.6mmHg。当压力小于4.6mmHg时,水只以固态和气态存在,不会随着温度变化发生改变。此时固态吸热(温度升高)后不经液态直接变为气态1。
根据热力学相平衡理论,当压力降到一定真空度,水的沸点和冰点就会重合,冰会直接变成水蒸气,即发生升华。即恒温时降低压力或恒压时升高温度都可以打破固、气两相平衡,使固态直接转变成气态;冷冻干燥就是根据这个原理进行的3,4。
冻干工艺过程及优化
药品冻干有5个步骤:准备好药液、冷冻、第一次干燥(升华)、第二次干燥(解析)、密封保存。
(1)准备药液:
一般配制成含固体物质4%~15%的稀溶液。如果固体含量过少,干燥过程中,药品微粒不能附着在基质上,会被逸出的蒸汽带到西林瓶的塞子上,甚至带到真空室中。
(2)冷冻
是一个恒压降温过程,使药液随温度的下降冻结成固体;使大部分溶剂(95%以上)冷冻成固体,形成一个最佳冰晶,促进蒸汽从固体骨架中扩散。
冷冻过程分为三个阶段,冷却阶段、相变阶段、凝固阶段。如下图所示:
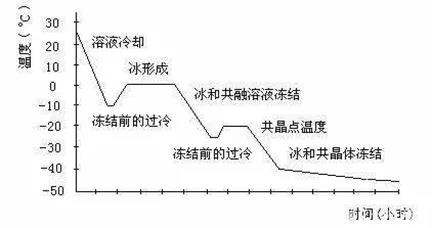
冷却阶段是药液从初始温度冷却到凝固点温度的阶段。在形成第一个冰核之前,药液保持过冷状态的程度叫过冷度。相变阶段是从第一个冰核形成和冰晶生长的阶段。凝固阶段是指所有冰晶都完全生长的阶段5。
其中共晶点温度是在冻结过程中,随着温度的降低,药液浓度较低,先从溶液中析出冰晶体,剩下的溶液则形成共晶溶液,水与溶质达到平衡。共晶溶液开始冻结的温度叫共晶点,是溶液完全冻结固化的最高温度。对溶液而言,冻结固化点就是熔化开始点,因此共晶点温度又称共熔点温度。在冻干技术中,将所有需要冻干的物料达到冻结时的温度称为共晶(熔)点温度6。
冻干箱的温度预先降到-50℃左右,预冻温度一般应为药品共熔点以下10℃~20℃。预冻时间通常在0.5h~2h。在药液放入冻干箱后可充入一定量的惰性气体维持真空度稳定。若预冻不完全,在减压过程中可能出现沸腾喷瓶的现象,使制品表面不平整。
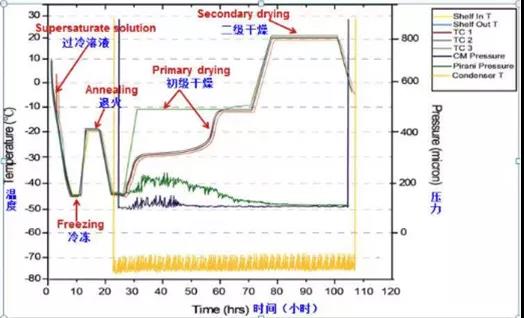
由于冻干过程比较快速,药液中的有些结晶成分不能完全结晶,如果该成分能为制品提供结构支撑或抗体在完全结晶后更稳定,那在升华干燥前必须将其完全结晶。可以将搁板温度提高到玻璃转化温度Tg之上,并保持设定的时间,这个过程叫退火4,5。因此预冻过程中要注意退火处理。
(3)升华干燥:主要是去除药品在冻结阶段形成的自由水(冰),大约80%~90%的水分。
首先要恒温减压,然后在抽气的条件下,恒压升温,使固态水升华。此阶段的升华温度应接近熔点温度,宜在共熔点温度下2~5℃,如果过低会降低升华速度。可以通过真空度、冷阱温度、控制搁板和药品温度来提高干燥速率。药品温度的控制标准是搁板温度的控制。药品温度在升华干燥过程中应小于20℃。
当冻干箱的压强<0.1毫巴时,箱内气体的对流传热可以忽略;而压强>0.1毫巴时,对流传热明显增强。升华阶段真空度在10~30Pa时,对于传递热量和升华均有利。
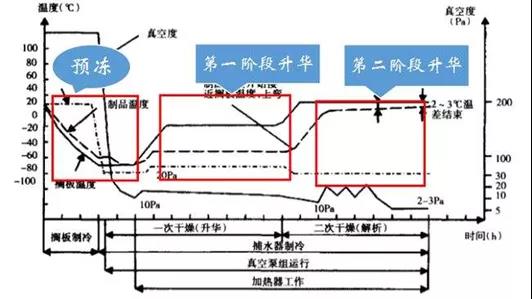
升华干燥阶段要注意制品的塌陷;
冻干产品在升华干燥阶段,随着升华时间的增长,产品出现已干层和冻结层,两层之间的交界面是升华面;升华过程中,升华面不断减小冻结层,不断增加已干层厚度。已干层结构疏松多孔,以便冻结层的水蒸气能逸出。但某些已干燥的产品当温度升高时,可能会失去刚性,变得有粘性,发生类似坍塌的现象。失去多孔结构,会堵塞升华时水蒸气的逸出通道;使升华速率变慢,搁板供给冻结层的热量有剩余,导致冻结层产品温度上升,当温度达到共晶点温度以上时,产品会发生熔化或发泡现象,此时的温度叫塌陷温度5,6,8。
有些产品崩解温度高于共晶温度,升华时只需控制产品温度稍低于共晶温度即可;对于崩解温度低于共晶温度的产品,以控制崩解温度为准。产品的崩解温度取决于产品本身的物性和保护剂的种类,优选具有较高崩解温度的材料,使升华干燥能在不太低的温度下进行,可以减少能耗,节约时间,提高生产效率。
一般来说,塌陷温度Tc比共晶温度Te稍高,共晶温度比玻璃转化温度Tg高;通常Tc比Tg高20K6。
(4)解析再干燥
物料中所有冰晶升华干燥后会留下许多空穴,仍残留约10%的水分。解析再干燥主要是去除未冻结的结合水(吸附在干燥的滤饼表面),使水分降低,维持在2%左右,得到干燥的物料,温度一般设置在25~40℃。
(5)密封保存
冻干结束后得到的干燥制品移出冻干箱后,要及时密封保存,否则接触空气后容易吸潮、萎缩。
冻干中会遇到的问题与处理措施1,7,9,10,11:
1. 含水量偏高
可能是西林瓶内药液过厚,升华干燥过程中供热不足,冷凝器温度偏高或真空度不足。一般药液厚度不宜超过12mm。
2. 制品外形不饱满或萎缩
药液浓度太高,冻干过程中内部水蒸气逸出不完全,冻干后,制品因潮解而萎缩,如下图所示。药液浓度过低,制品疏松易引湿,又因为比表面积大,使制品也易萎缩。一般药物的浓度在2%~30%为宜,在10~15%最佳。
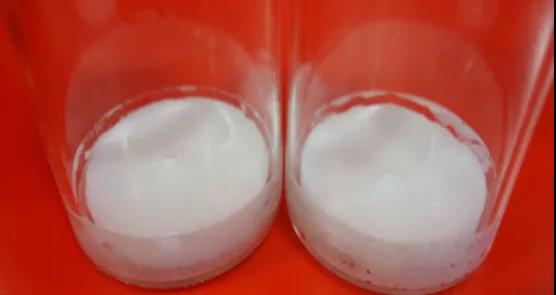
3. 喷瓶
喷瓶原因主要有三方面即药液中的气泡、预冻不完全、供热太快导致的受热不均匀。
气泡-制品在分装过程中,由于液体流速较快,在瓶内产生一定量的气泡,应将装瓶液体放置一段时间让气泡逸出,否则气泡被冻结在制品内部,当升华过程抽真空减压时,气体逸出会带出部分制品黏附于瓶壁上。
预冻不完全-冻结过程预冻温度不够低或保持时间不够长,未能使溶液全部固化,真空升华干燥时,溶液的温度至共晶点时,溶液和水同时结晶析出,液体沸腾,造成喷瓶。控制预冻温度比共晶点温度低15℃保持2-3h,确保完全冻结。
供热过快、制品受热不均匀-升温过快造成制品受热不均匀,下层的制品的结晶不会直接升华,而是从固体、液体到气体蒸发,导致喷瓶。因此要控制升华干燥阶段特别是在共晶点附近的升温速率,均匀且不宜过快。
4. 冻干后pH发生偏移
一般处方中含有挥发性酸和不挥发性碱,pH会升高;有不挥发性酸和挥发性碱,pH会降低。可以在溶液中添加缓冲溶液避免pH偏移。
5. 制品表面有硬壳、突起、裂面
硬壳-冻结时产品表面形成不透气的玻璃样结构,升华干燥开始后产品升温,部分产品发生熔化收缩,使表层分裂,下层的升华正常进行,上层形成硬壳,解决方法是在预冻时做退火处理。
裂面-由于固体物质浓度过低,产品块的结构脆弱所致。可以减慢再干燥的速度来限制物质的损失,或者增加整体赋形剂的浓度来加强产品块的结构。
突起-产品在冻结时可能会有一个从粥状到固化的过程,固化时体积膨胀对粥状冰由四周向中间挤压,在制品表面形成一个尖状突起。这与处方和预冻时降温过快有关,有些冻干保护剂容易形成这种小突起,可以通过更换冻干保护剂或改变预冻方式来解决。
注:上述图片均来源网络
参考文献
1. 第七版药剂学.
2. 万军等,制剂药品的冻干原理及技术.
3. 任红兵,真空冷冻干燥技及其在中药领域的应用
4. 殷洪玉等,冷冻技术在制药工艺中的应用.
5. 勒力等,冷冻干燥技术及冻干抗体药物的研究进展[J],聊城大学学报.
6. 徐成海等,冻干技术的几个热点问题,第十届全国冷冻干燥交流会论文集.
7.王义飞等,制剂药品的冻干原理及技术.
8.蔡亲,药品冻干工艺技术研究.
9.王键,冻干技术中常见的问题和解决办法[J],江苏药学与临床研究.
10.药品冻干过程中常见问题产生的原因及解决方法,PharmTEC制药网/技术
11.冻干品外观之十四种缺陷与原因解析,丁香通
<END>
收藏
登录后参与评论